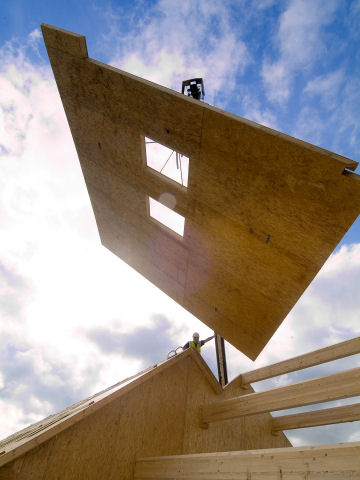
Structural Insulated Panels
So what are SIPS.
Structural insulated panels (SIPs) have been around for quite a while, yet still unheard of by most people. Looking at the specs, we find them hard to ignore as a important part of building a highly insulated home.
Basically, SIPS are like foam board, rigid foam sandwiched between two wood panels. Just like foam-board, the result is a material that has improved structural properties. The foam become protected by the outer sheets, and the outer sheets gain tremendous rigidity vs just plain flat wooden panels.
Have you ever looked at the building blocks of foam-board? The Styrofoam by itself is a bit spongy, and can break into pieces if bent too far past its flexible range. Thin paper sheets, we all know how flimsy they are on their own. No glue them down to both sides of the foam and the result is a new material that is suddenly far more rigid, no longer easily snaps, the foam is protected from chipping away, and is solid enough to cut up into shapes and create solid forms.
Now imagine the foam is 5-12” thick, add to that 1/2” thick sheets of osb wooden sheets, glued across the entire surface on both sides. The result is an extremely rigid panel capable of supporting a car without any significant flex, The finished panel has structural properties that exceed those of its parts.
Panels can be compared to I-beams. I-beams are an engineering structural component. Take a long piece of wood or metal a half inch thick and try to bend it, it will easily bend. If you take two pieces, and join the third piece vertically between them, the result is a beam that has significantly increased resistance to bending. The taller this "web plate" in the center, the more rigid the beam becomes to bending without adding much material or weight.
In many ways, a sandwiched panel gains the properties of an I-beam. The sheets behave like the top and bottom flanges, and the foam center acts as the web plate. The thicker the foam in the center, the more rigid the structure. The incredible thing is that foam is so light, that it hardly contribute much mass to the structure as you add thickness. The critical detail for this i-beam rigidity is the bond between the three components must be extremely strong. The two flanges and center web material must behave as one unified structural member. As long as there is no slipping or breaking of the bond between the 3 pieces, the panels are incredibly rigid and can easily carry the loads typically found in home construction.
As a building material, the foam core brings more than just thickness to the scene. Foam is an incredible insulator. Just look at disposable cups. Take a simple Styrofoam cup, hardly 1/8” thick , and add boiling hot coffee into it and pick it up comfortably. Try doing that with essentially all other cups, and there is no comparison. 1/8” thick foam can keep 200+ degrees liquid temperature from reaching the outside surface. Image what it would do if it was an inch thick, or 2” , or 12” !
We will be looking at these panels in greater detail and compare them with other concepts such as double wall construction.
Do you live in a home built with SIPS? We welcome your feedback.
Comments